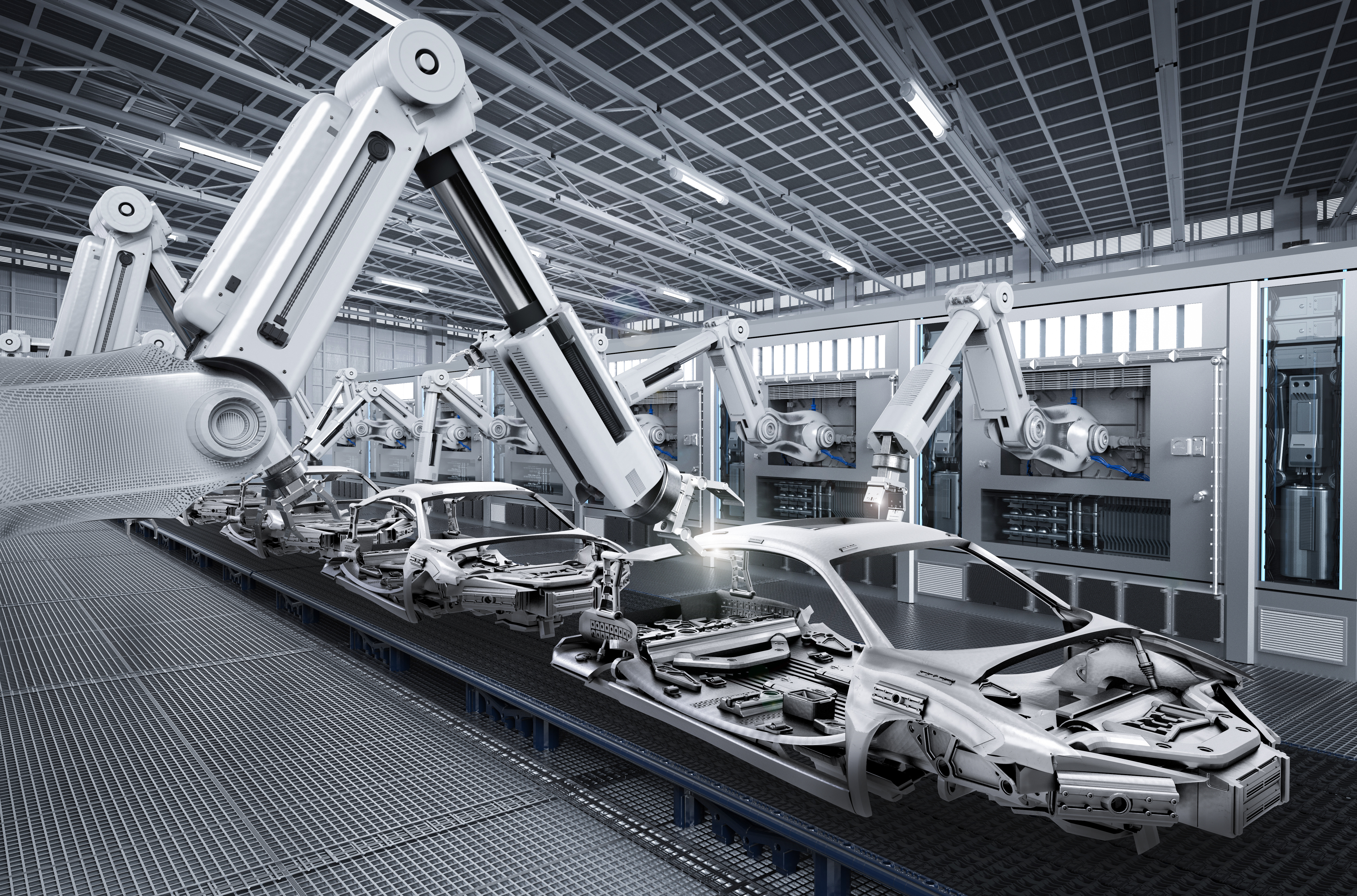
Leading European automotive company monitors automation robots with Intellinova Parallel MB
Status Pro Maschinendiagnostik, distributor of SPM condition monitoring solutions in Germany, has been entrusted to deliver online measuring equipment to one of the leading automotive manufacturers in Europe. Following a comprehensive field test at the beginning of 2018, Intellinova Parallel MB was chosen as the most cost-efficient and reliable solution for monitoring the mechanical condition of mobile automation robots.
Germany, the leading producer of passenger cars in Europe, delivered over sixteen million vehicles in 2017. Because of the competitive nature of the automotive industry, the profit per car is small, and the number of cars produced is vital. Due to the tight margins, a single unplanned production stop may have severe economic consequences.
This major German car manufacturer had issues with the rails on the mobile automation robots, which carry out both cutting and welding of car parts and assembly. Damaged rails cause interference in the robot’s movement, in turn causing pre-programmed jobs to be carried out at the wrong time and place. The car manufacturer needed a reliable monitoring solution to avoid these production disruptions. After a one-year pre-study in which different types of condition monitoring methods were compared, the car manufacturer decided that SPM’s measuring techniques were to be further evaluated.
Status Pro Maschinendiagnostik was contacted and successfully completed a field test as well as a three-month pilot on ten automation robots at one of the car manufacturer's sites. Intellinova Parallel MB, a small and robust unit for parallel condition measurement on four channels using the DuoTech accelerometer, was the perfect solution. In addition to providing simple and clear results on the condition of the machines, the measuring unit is also cost-effective; an essential factor as there are over 1.700 robots in this particular facility.
In a solution tailored to customer needs, the measurement data is delivered from the measuring units straight into the customer’s PLC, where trends and alarms can be monitored. More in-depth analysis is made possible by transferring the data from the PLC to the Condmaster Ruby diagnostic software using the OPC communication protocol.
During the three-month pilot, two bearing damages were successfully identified on two of the automation robots and later verified by an external bearing fatigue laboratory. Following the successful pilot, the condition monitoring solution was installed on the first batch of one hundred automation robots. More installations will follow at the manufacturer’s sites around the world.
Wilhelm Bachmeier, Managing Director of Status Pro, commented: “I am very pleased that all our hard work has paid off. For us, this is the first step away from classical condition monitoring on ventilators in the paint section, into production with its high demands on the availability of machines and the complexity of measuring the condition of an automation robot. For our customer, it is essential to avoid losses of production time and be able to plan maintenance and service in advance to meet their production goals.”